Our Services
Specialized oilfield inspection services ensuring safety, compliance, and operational reliability.
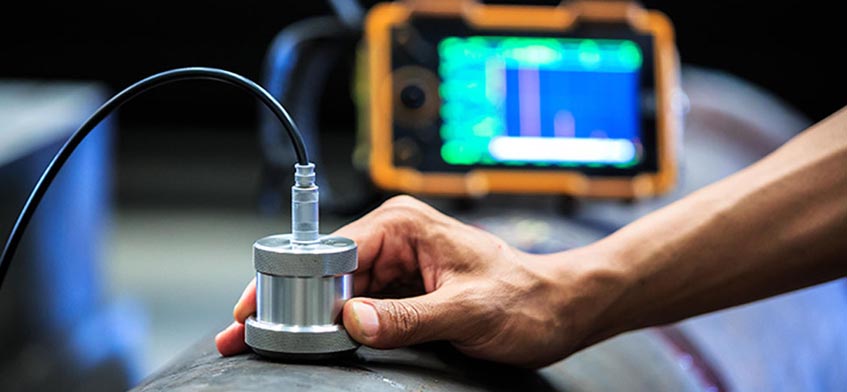
NDT
Comprehensive Non-Destructive Testing (NDT) Services by OIS
At Oilfield Inspection Services (OIS), we understand that asset integrity is at the heart of every successful operation. That’s why we provide a complete suite of Non-Destructive Testing (NDT) services tailored to support the entire lifecycle of your equipment—from fabrication and in-service inspection to decommissioning. Our goal is to help you identify and manage potential issues before they evolve into costly or hazardous failures.
Whether you're building new infrastructure, maintaining existing assets, or retiring aged equipment, OIS has the expertise and tools to deliver accurate, efficient, and reliable testing solutions. Our NDT services play a crucial role in the overall integrity appraisal process, giving our clients the insights they need to make informed decisions that protect their investments and ensure operational safety.
We offer a broad range of standard and advanced NDT methods, each designed to meet specific inspection requirements. These include, but are not limited to:
Ultrasonic Testing (UT)
Magnetic Particle Testing (MT)
Liquid Penetrant Testing (PT)
Radiographic Testing (RT)
Eddy Current Testing (ECT)
Phased Array Ultrasonic Testing (PAUT)
Time of Flight Diffraction (TOFD)
Each technique is performed by our certified technicians, using the latest industry-grade equipment to ensure accuracy and efficiency. Our services are compliant with international standards and are customized to meet the specific needs of industries such as oil and gas, energy, petrochemicals, construction, and manufacturing.
Magnetic Particle Inspection otherwise known as MPI is a method that can be used to find surface and near surface flaws in ferromagnetic materials such as steel and iron it is primarily used for crack detection.
Magnetic particle testing works by magnetizing a ferromagnetic specimen using a magnet or special magnetizing equipment. If the specimen has discontinuity, the magnetic field flowing through the specimen is interrupted and leakage field occurs. Finely milled iron particles coated with a dye pigment are applied to the specimen. These are attracted to leakage fields and cluster to form an indication directly over the discontinuity. The indication is visually detected under proper lighting conditions.
The basic procedure that is followed to perform magnetic particle testing consists of the following:
Pre-cleaning of component
Introduction of Magnetic field
Application of magnetic media
Interpretation of magnetic particle indications our experienced and qualified NDT inspector.
Dye Penetrant Inspection, also known as Penetrant Testing (PT), Liquid Penetrant Inspection (LPI) or Fluorescent Penetrant Inspection (FPI).
Liquid penetrant is applied to the surface and left to soak, being drawn into any cracks by capillary action. Excess penetrant is then removed and a developer applied to draw out the penetrant from cracks, to enable a visual Inspection of any defects. Accurate interpretation is achieved by utilizing our seasoned NDT qualified Penetrant Testing Inspectors.
Dye Penetrant Inspection can be used on almost any non-porous material.
The types of defects that can be found with penetrant testing are:
Rolled Products: Penetrant identifies anomalies (cracks, seams or laminations)
Forgings: Illuminating cracks, laps or external bursts.
Welds: To identify cracks, porosity, undercut, overlap, lack of fusion or lack of penetration.
Most of our customers are consistently opting for Eddy current testing due to inherent benefit of non-requirement of paint removal prior carrying out Inspection on a system which is a drawback in the conventional NDT method of MPI. Eddy current testing eliminates the need of surface preparation and saves lot of time in paint removal and re-application of paint post Inspection. Typical site applications include Inspection of crane jibs, pedestals, pad-eyes (pre and post loading), drilling derrick substructures and wind turbine towers.
Eddy Current Testing is sensitive to small cracks and other defects. Inspection gives immediate results and detects surface and near surface defects.
OIS uses the latest sets of state of the art Eddy Current Testing for Inspection.
As this is an advanced NDT method of Inspection, skill and experience are required. With over 10 years of experience in this field we are able to understand the Inspection readings.
We have available more than twenty (20) experienced ET technicians that are SNT Level II Eddy Current Testing qualified in compliance with SNT-TC-1A. As a minimum, all OIS Eddy Current Inspection engineers have more than one NDT qualification.
Visual Inspection, with or without visual aids, is the original and still highly effective method of NDE. Many defects can be detected by careful direct visual Inspection. Optical aids used include low power magnifiers, microscopes and telescopes. Borescope’s, endoscopes and other fiber-optic devices are used for Inspection of areas with restricted access. These devices can be used with television camera systems. High-speed visual Inspection may be used for tubular components.
Ultrasonic Testing uses sound waves of short wavelength and high frequency to detect flaws or measure material thickness as an NDT method. Ultrasonic Testing is used to test welds, castings and wrought products such as rolled plate or forgings.
The detection and location of discontinuities is enabled by the interpretation of ultrasonic wave reflections generated by a transducer.
Information from ultrasonic Inspection can be presented in a number of formats:
A - Scan displays the amount of received ultrasonic energy as a function of time
B - Scan displays a profile view (cross-sectional) of a specimen
C-Scan displays a plan type view of the specimen & discontinuities
The relationship of flaw size, flaw distance and flaw reflectivity are complex and considerable skill is required to interpret the display. With over 10 years of experience in this field we are able to understand and give actual interpretation of Inspection exercise.
We have available more than thirty (30) experienced UT technicians that are SNT Level II Ultrasonic Testing qualified in compliance with SNT-TC-1A. As a minimum, all OIS ultrasonic testing Inspection engineers have more than one NDT qualification.
EMI 1 Inspection method is applied to drill pipe tubes. It involves full length scanning (excluding upsets) of drill pipe tubes using the longitudinal field (transverse flaw) buddy type unit. Evaluation includes flaws such as fatigue cracks, corrosion, pits, cuts, gouges, and other damage that exceed the specified acceptance limits.
OIS can provide full range of pipe Inspection ion sizes ranging from 2-3/8" to 6.5/8" while following customer's specifications and edition of DS-1 or API guidelines. We have state-of-the-art tube Inspection equipment to meet API Inspection requirements or third party inspections, including full-length wall thickness measurement of the pipe tubes. Also have various types EMI of units, conventional ones as well as dual-function units with wall monitoring.
Inspection services includes:
Visual body and thread Inspection
• UT Thickness Gauging
• Thread gauging
• End Area Inspections
• Electromagnetic Inspection (EMI)
• Ultrasonic Inspection On End Area
• Wet and Dry Magnetic Particle Inspection
• Dimensional Inspection
We also can provide refacing, straightening and pipe internal and external cleaning services.
Used casing and tubing Inspection is carried out in accordance with API Spec 5CT. The general scope shall include:
• OD Blasting
• ID Cleaning
• Spot Wall Thickness Measurements
• Grade Sorting
• EMI on Body (Tubing)
• Visual Thread Inspection
• Full Length Drifting
• Black Light Inspections
• Hydraulic Pressure Testing
• Bucking Services
Depending on client’s requirement, the general scope or part of the scope may be covered. Our experienced inspectors follow industry standard guidelines and documented Standard Operating Procedures for casing and tubing Inspection.
OIS state of the art EMI units are dual-function units with Hall Effect sensors. As they are all mobile units our Inspection technicians are able to move units to work locations at short notice.
OIS state of the art EMI units are dual-function units with Hall Effect sensors. As they are all mobile units our Inspection technicians are able to move units to work locations at short notice.
We provide BHA Inspections on any drilling component used in the industry.
Bottom Hole Assembly otherwise known as BHA inspections are carried out as per latest editions of DS-1 Cat 3-5 and API guidelines. BHA inspections services include:
• Visual Inspections
• Thread Gauging
• Wet and Dry Magnetic Particle Inspection
• Dimensional Inspection
Optional service of refacing if required can be provided.
We have fleets of BHA Inspection units that are available in our tubular goods Inspection facility and can also be moved to clients’ facility.
Upon completion reports are generated and made available on web for ease of access to our customers who usually are given unique password as part of the Inspection package. Hard copies could also be given upon request.
Our comprehensive rod Inspection and reconditioning services are performed according to API standards. Rod Inspection helps reduce well operating costs by extending the life of the rod and minimizing the risk of future well failures.
A large valve at the top of a well that may be closed if the drilling crew loses control of formation fluids. By closing this valve (usually operated remotely via hydraulic actuators), the drilling crew usually regains control of the reservoir, and procedures can then be initiated to increase the mud density until it is possible to open the BOP and retain pressure control of the formation. BOPs come in a variety of styles, sizes and pressure ratings. Some can effectively close over an open wellbore, some are designed to seal around tubular components in the well (drillpipe, casing or tubing) and others are fitted with hardened steel shearing surfaces that can actually cut through drillpipe. Since BOPs are critically important to the safety of the crew, the rig and the wellbore itself, BOPs are inspected, tested and refurbished at regular intervals determined by a combination of risk assessment, local practice, well type and legal requirements. BOP tests vary from daily function testing on critical wells to monthly or less frequent testing on wells thought to have low probability of well control problems.
Quick Fact
Have questions or need expert inspection solutions? We’re here to help. Reach out to Oilfield Inspection Services for reliable, certified, and timely inspection support.
CALL TO ACTION